First, the application of open CNC CNC The application of CNC technology has brought profound changes to the manufacturing industry, but with the rapid development of computer technology, the traditional CNC system has gradually shown its main weakness, that is, the system software is a manufacturer. All of this makes the traditional CNC system more specific and less versatile, does not enable functional extensions and various kinds of software support, updates, poor software portability, poor networking communication capabilities, and more stringent requirements for machine tool manufacturers and users. higher. The development of modern manufacturing industry places higher demands on the CNC system. From the perspective of completeness of functions, on the one hand, CNC systems must adapt to the development of DNC, CAD/CAM and CIMS, and there is a platform that can integrate software provided by different developers and suitable for networking needs; on the other hand, with the trend of small and medium batch sizes With the increasing number and application of numerical control systems in the information, automotive, metallurgy, textile, printing, and military industries, a user-oriented control system must be constructed quickly, efficiently, and cost-effectively according to different user needs. This requires the CNC system to be modular and reconfigured. From a usage perspective, the new CNC system should be able to be used on various computer software platforms, and provide a unified style of user interaction environment to facilitate the user's operation, maintenance and replacement. This requires the CNC system must try to get rid of its traditional closed mode and develop in an open direction. PC-based open CNC systems are the embodiment of this development direction. NC open or PC-NC refers to a PC-based open CNC system. Specifically, it is possible to easily use the software modules and hardware motion control plug-in cards provided in the system on the operating system of the popular personal computer, so that machine tool manufacturers and users can easily perform software development, add functions, and realize Functional personality. Here the traditional CNC system combines the PC's high-speed analysis and computing capabilities, large-capacity storage capabilities, the support of various commercial software, graphic display advantages and networking flexibility, making the traditional CNC system has an open model. In the early 1980s, Open CNC began to promote open PC-based CNC systems, but it was not until the early 1990s. Research on open CNC systems began in 1987 when the U.S. Air Force published a well-known “Next Generation Controller Next Generation Controller†research program under US government funding. It first proposed the concept of an open architecture controller. One of the important contents is the "Open System Architecture Standard Specification (OSACA)". Since 1996, several large scientific research institutions in the United States have published corresponding research contents on the NGC plan. For example, under the support of the US Navy, the U.S. International Standard Institute proposed the "EMC (Enhanced Machine Tool Controller)"; The OMA, Ford and Chrysler three major automotive companies proposed and developed "OMAC (Open Mode Architecture Controller)"; it is very similar to the EU "OSACA (Open Architecture for Automation Systems)". The OSACA project of the European Union is under the auspices of the Institute of Machine Tools and Devices of the University of Stuttgart, Germany. The relevant institutes, universities and manufacturers in 11 countries including Germany, Italy, France, Switzerland, Britain, and the West have developed an open CNC system. Standards, the system is based on the PC as a standard platform, plus a freely combinable software module, and is structured as an “open controller that does not depend on a specific vendorâ€. The "controller" referred to here does not only refer to an NC device, but includes a robot controller, a PLC, a unit controller, etc. to realize a free combination of software modules. DSP-based Motion Control Technology and Open CNC In today's automation technology, motion control represents the most versatile and complex task. The reason is that the speed of the production process is constantly increasing, and the manufacturing industry has made increasingly higher demands on machining accuracy and agile manufacturing. Open CNC has been subject to the limitations of PC computing capabilities, making it difficult to achieve a more complex control algorithm, hindering the development of such systems to high-speed, high-precision direction, but in the late 80s based on DSP (Digital Signal Processor) motion control technology The breakthrough provides an excellent opportunity for the open CNC. Now the open CNC is based on the DSP motion controller as the core, the integration of PLC functions, and integrated with the universal industrial PC. It can also be said that there is no real open CNC without DSP-based motion control. At present, the product suppliers of motion controllers are mainly foreign companies such as Delta Tau, Galil Company, Dspace, and Movtec Company in the United States. The advantages of using a DSP-based motion controller plus a PC to form an open CNC are many. Open CNC can combine WINDOWS's powerful graphical user interface, multitasking capabilities, and powerful hardware and software compatibility with the unmatched servo, interpolation, and real-time computing capabilities of DSP-based motion controllers to provide users with high-speed, high-precision In addition to the low-cost modern control, in addition, the open CNC based on the DSP not only combines the functions of the traditional CNC, but also provides the functions that the traditional CNC cannot provide. See the attached table for a comparison of the new open CNC with traditional CNC.
Attached Table: Traditional CNC vs. Open CNC Comparison Project Traditional CNC Open CNC Software Inheritance Each time a new CNC is introduced, the software needs to rewrite the software with modular features, improve CNC performance without rewriting software software development Difficulty must use special software developed by CNC manufacturers, and the amount of development time is huge. The core processing part has become a "black box." Closed software with high-level language and advanced integration environment such as Visual C++ programming software is used by CNC manufacturers. It is difficult for machine tool manufacturers and users to demonstrate their independence. Machine manufacturers and users can easily develop application networks with individual application software. Consistency includes manufacturer's special hardware and communication methods, networking costs are high, and special equipment and special technology are required for networking. Field buses such as CAN, PROFIBUS, etc., as well as INTERNET, etc., are easy to implement, and networking requires future development of dedicated hardware. Following the progress of technology, generally open and modular after relative broadcasting, standardization, convenient for secondary development, system function, single application, multiple application and cost performance, applicable to the machine tool industry, good cost performance applicable to all machinery industries including machine tool industry, and cost performance The good movement execution part adopts the special servo interface, can only use the standardized and generalized servo interface of the product of the specific manufacturer, can choose the drive device and the CNC function of the motor to triaxial or multi-axis interpolation, the speed is fast and multi-axis drive, much Shaft interpolation, faster speeds, foreign CNC developers are in the product Developed above an open CNC, it is known as the sixth generation of numerical control system. China has recently begun to introduce this technology. Currently, it is still in the stage of introduction and digestion and is developing a system with its own intellectual property rights. Second, the modern network manufacturing technology network technology and manufacturing from the open CNC is based on personal computer PC numerical control system, network technology is also known as the third milestone in the history of computer development, people say that the network is a computer, profoundly It reflects the extremely important role and influence of the Internet in the history of computer development. In the 1980s, with the rapid development of the local area network LAN and the world's largest Internet INTERNET, which was created by the development of the emblem machine, the computer was no longer a stand-alone device. It had become the basic equipment connecting the entire society, and With great impetus to change people's lives and production methods. Therefore, it is inevitable that the network will enter the manufacturing industry. It will bring a brand-new development to the traditional manufacturing industry, and it will increasingly show its superiority. According to foreign sources, the entry of the Internet into the workshop is a "revolution of the factory process." Therefore, the model of network manufacturing, a model of modern manufacturing technology, has become more and more important for the manufacturing industry. In a broad sense, network manufacturing is represented by the use of networks between companies and enterprises for cross-regional collaborative design, collaborative manufacturing, information sharing, remote monitoring, and remote services; supply, sales, and services between enterprises and society. In the narrow sense, it is expressed as the internal network of the company, the internal management department (production, supply, sales, human, financial, material, etc.), design department (CAD/CAM/CAPP/CAE, etc.), production department (production management , production monitoring, knives, clamps, quantities, material management, equipment management, etc.) are integrated under the support of a network database. The application of these technologies has greatly increased the productivity of the manufacturing industry. For example, CNC machine tools using networked technology demonstrated at the 2000 International Machine Tool Show in Chicago can increase the utilization rate of machine tools from 25% to 65%; for example, Ningxia Xiaojuren Machine Tool Co., Ltd. was established in May 2000. (China and Japan Yamazaki Mazak joint venture established) using MAZAK intelligent network manufacturing model, the company employs 135 people, annual production of vertical machining centers and 420 CNC machine tools, per capita output value of 1.6 million yuan or more, such a high productivity Mainly due to the use of intelligent network manufacturing systems. Open CNC and network manufacturing In the modern network manufacturing environment, machine tools (here index-controlled machine tools, machining centers, flexible manufacturing units, etc.) are no longer isolated processing equipment, but the network environment and CAD/CAM/CAPP/CAE. Engineering design system The MRP management information system is directly connected to a node that has processing capability. It must communicate with the related external environment such as the management information system and the engineering design system through the network, and must realize two-way communication between each other. The management information computer can send processing instructions to any one of the CNC machine tools, real-timely check the processing programs, processing status, processing time, and fault signals of each machine tool, and each machine tool can also report the situation to the management information computer, such as processing. The number of cases and results, qualified products, and waste products allow the management information computer to analyze problems and solve problems, and achieve a dynamic reconfiguration of processing routes. The engineering design computer uses CAD/CAPP/CAM technology to generate CNC machining programs that are transmitted over the network to the machine tool for CNC machining. Paperless manufacturing. Currently, traditional CNC systems generally do not have direct networking function. Therefore, the CNC system must first be connected to a general-purpose computer through a point-to-point serial communication line (usually using a serial interface such as RS232 or RS485), and then it will have networking functions. The PC is connected to the local area network. In this scheme, although the PC is used as a bridge to realize the networking of the CNC, the serial communication speed between the CNC and the PC is low and the reliability is poor, which becomes the bottleneck of information transmission in the system. On the other hand, it has increased the PC and expanded the system hardware scale. This not only increases the system cost, but also increases the failure rate and adversely affects the reliability of the system. PC-based open CNC systems, because of the use of standard PC hardware and standard operating systems, have their own direct networking capabilities. It provides a best platform for network manufacturing systems. The true meaning of the network manufacturing system is precisely the combination of the two. In PC-based open CNC, because the hard disk is used as the storage carrier of processing code, the CAD/CAM calculated processing program can be transmitted to the CNC hard disk at one time through the standard network. The standard network speed is generally tens of Mbps ( Serial interfaces such as RS232 and RS485 are generally only a few tens of kbps, which increases the data transmission speed by a factor of several thousand. The previous transmission before processing ensures the reliability of system transmission. Because of the large capacity of the hard disk and the fast reading and writing speed, even if the code of a straight segment with a length of 0.01 mm in length is used, the processing speed of the CNC at a pulse equivalent of 1 μ can reach hundreds of meters per minute. This is a speed that traditional CNC systems using serial interfaces such as RS232 can't reach. This solves the problem of high-speed, high-precision machining of large programs, and eliminates the need for surface and spline interpolation, which reduces CAD/CAM. System burden. If the resolution is increased to 0.1μ, the CNC processing speed can reach more than ten meters per minute, which greatly smoothes the movement of the machine tool, improves the surface finish, reduces the machining surface error, and achieves high-speed and high-precision machining. . The development and application of network manufacturing system in China Since the 1990s, with the support of network technology, firstly in the United States and then in other developed countries, agile manufacturing enterprises of network manufacturing systems have been developing rapidly, and universities and research institutes and enterprises in China have also advanced. In this direction, China's information technology and network are currently used in the following four modes of development in modern manufacturing enterprises: The application phase of cell technology is characterized by the use of computers, the use of software, numerical control devices are scattered, and information is not directly interactive Information islands. The specific performance is: The management department uses specialized software such as finance, personnel, marketing, and warehouses according to their functions; the design department uses CAD, CAPP, CAM, and other software; and various CNC and automation equipment are used in the production department. The business coverage of this model is very wide, and many companies have a long history and a certain level of application. The local integration stage is characterized by the establishment of a local area network and the integration of various decentralized application units by departments, but there is still information isolation and information bottlenecks. The specific performance is: the management department and the design department establish a unified platform and database, respectively, using commercial integrated software system, which includes the functions can cover the department; in the production sector, the performance of CNC equipment networking and even plant-level management. This type of application has been gradually recognized and applied by many companies, but it has not been a long time. It is currently the most demanding category. The internal integration of the enterprise establishes a large-scale database and interconnects and shares information among various functional departments. Flatten the original pyramid management model to reduce intermediate links. At present, few domestic enterprises have reached this model and have not yet reached a mature stage.

The drawings have reached the broad stage of network manufacturing, ie, the interconnection between enterprises and enterprises, enterprises and society, and information sharing. At present, only a very few domestic enterprises have begun to enter this model, such as Ningfu Little Giant Machine Tool Co., Ltd. Now taking Ningxia Little Giant Machine Tool Co., Ltd. as an example (see the attached figure), the factory is known as a smart networked machine tool factory, and it covers the entire company's so-called intelligent network, which is Ethernet. The CNC machine tools and FMS of the company's machining shop all use open CNC, and they can all be directly connected to Ethernet. They are first connected via Ethernet to computers that are responsible for NC programming, production scheduling, tool fixture management and process monitoring. Integration of manufacturing processes at the shop floor. Based on this, the company's CAD, MRP, and other subsystems are further connected via Ethernet to integrate the entire company's information. Then through the INTERNET network to achieve resource sharing between companies, portfolio and conduct e-commerce. The plant is known as the second intelligent network machine tool factory in the world. While many research institutions are still experimenting with and authenticating this game, Little Giant Machine Tool Co., Ltd. has perfectly combined information technology (IT) and traditional manufacturing (MT) in the entire production and management process. A model of network manufacturing. 3. Conclusion With the development of computer technology, PC-based software support has improved and matured. The operating system has good reliability, compatibility and openness. The traditional CNC will eventually be replaced by the PC-based open CNC. This is unavoidable. We should seize this opportunity to keep up with the development trend of the world's numerical control technology, catch up and narrow the gap between the digitally controlled city and advanced countries. Manufacturing industry is the foundation of the national economy. The core of modern manufacturing technology is the successful occupation of computers and network technologies. The developed countries' network manufacturing technologies, virtual manufacturing, and agile manufacturing enterprises have developed rapidly. In the direction of industrial development announced by the U.S. government not long ago, the operating system and hardware structure of a general-purpose computer have been clearly defined as two important contents of manufacturing technology. It can be expected that the advanced manufacturing technology supported by computer and network technology will be the demand for the rapid adaptation of the manufacturing industry to the market, constantly launching new products, gaining competition, and obtaining the main direction of survival and development. Network manufacturing is especially in line with China's national conditions. It does not require large investment, and output is very significant. China's scientific research departments and enterprises should vigorously develop in this direction.
Roller Shutter Door and Door Frame Forming Machine
This door frame machine is designed according to cutstomer require. One machine can produce same profile but different sizes. It saves lots of cost, and get customers great satification.
The shutter door machine has many type of design. The austrilia type use wide raw material width, and easy to make the door. The small type of shutter door strip has nice appearance, and durable product. Besides, there are some other type of shutter door machine, like anti-wind shutter door machine and fire proof shutter door machine. The fire proof shutter door machine has the steel frame with EPS inside.Such as steel door frame making machine.
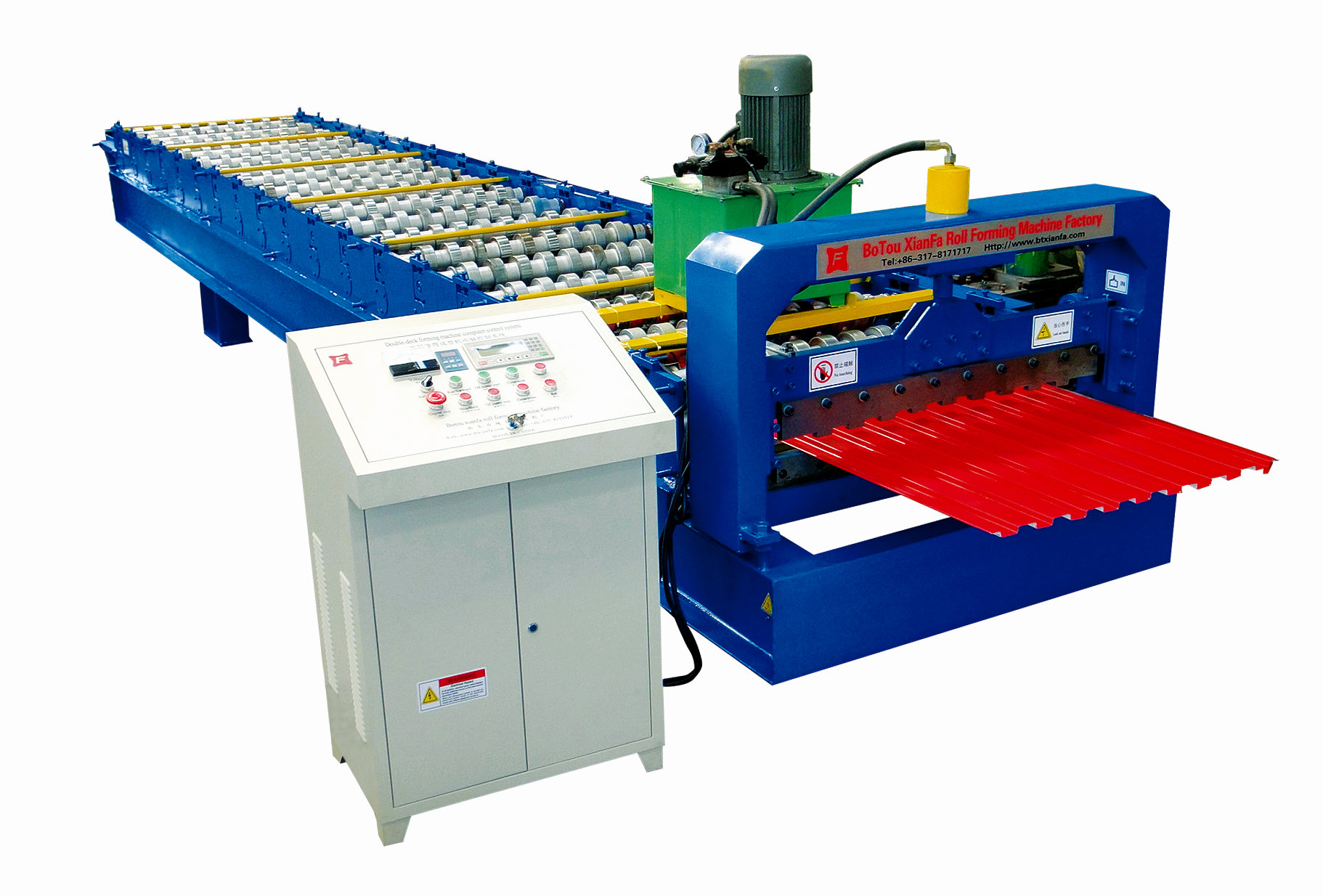
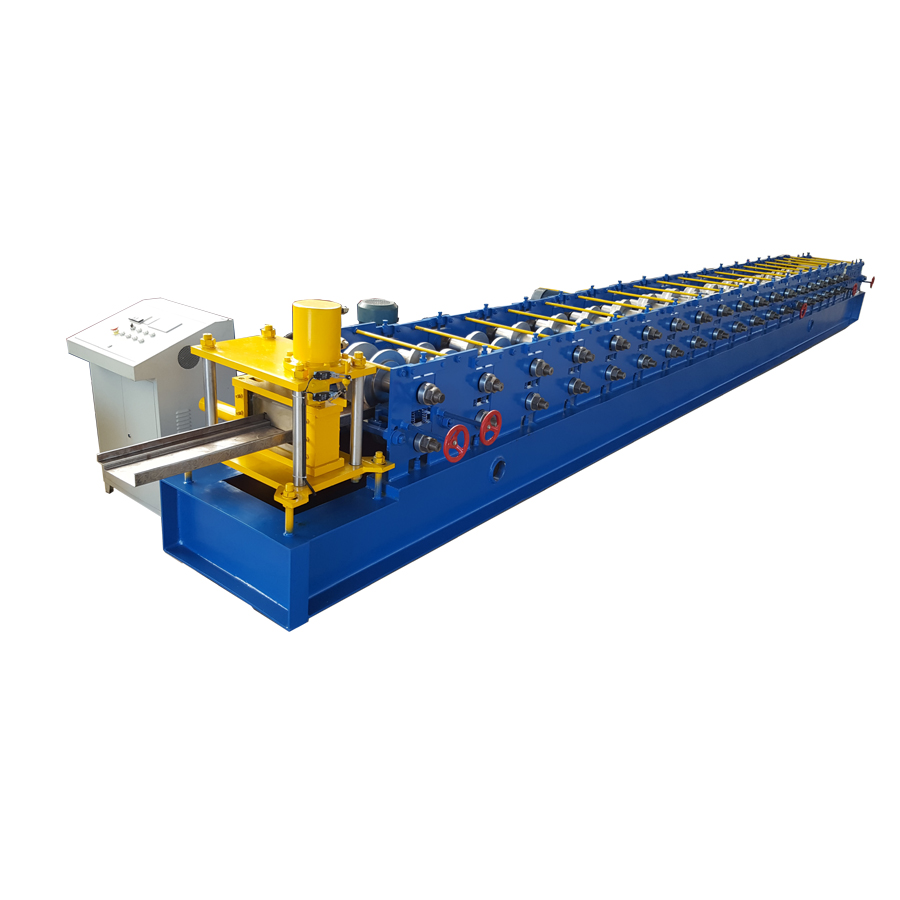
Roller Shutter Door and Door Frame Forming Machine Series
Roller Shutter Door Forming Machine,Door Frame Forming Machine,Door Frame Roll Forming Machine,Shutter Door Roll Forming Machine
Botou Xianfa Roll Forming Machine Factory , https://www.rollformingmachinecn.com